Retreaded tires reduce natural resource extraction, land use, carbon emissions, air pollution, and water consumption. Continental Tire also gives new life to truck and bus tires to realize the full economic performance of the tires. It’s a multi-stage process that requires bead-to-bead precision, robust durability and safety tests to ensure warrantied quality.
The 13 dealers in the United States offering Continental’s retreading services rely on a proprietary application to track every step in the process. Yet, when the legacy platform proved cumbersome, Continental turned to Dualboot Partners to provide the necessary flexibility in a new app with the same fresh finish as its end product tires.
The opportunity
With retreaded tires helping fleets reduce costs and ensure higher mileage, building up the retread business is a key part of Continental Tire’s growth strategy in the U.S. market. To make its network of ContiLifeCycle tire locations more efficient, Continental needed to revamp its application for each of its network partners.
Continental wanted to improve the design and user experience of its software. Recognizing that some tires need to go to different stations in the multi-step process (but perhaps not all of them), the company wanted to improve the flow between stations. Doing away with the login process and simplifying the user interface in other ways would help.
Additionally, Continental wanted the new software to automate order entry and reporting functions. Enhancing these functions required adjustments to the database model so that information could be accessed without custom queries.
Dualboot’s team was happy to take the driver’s seat in rebuilding the existing application on a new platform with further enhancements, additional security, and a refreshed look.
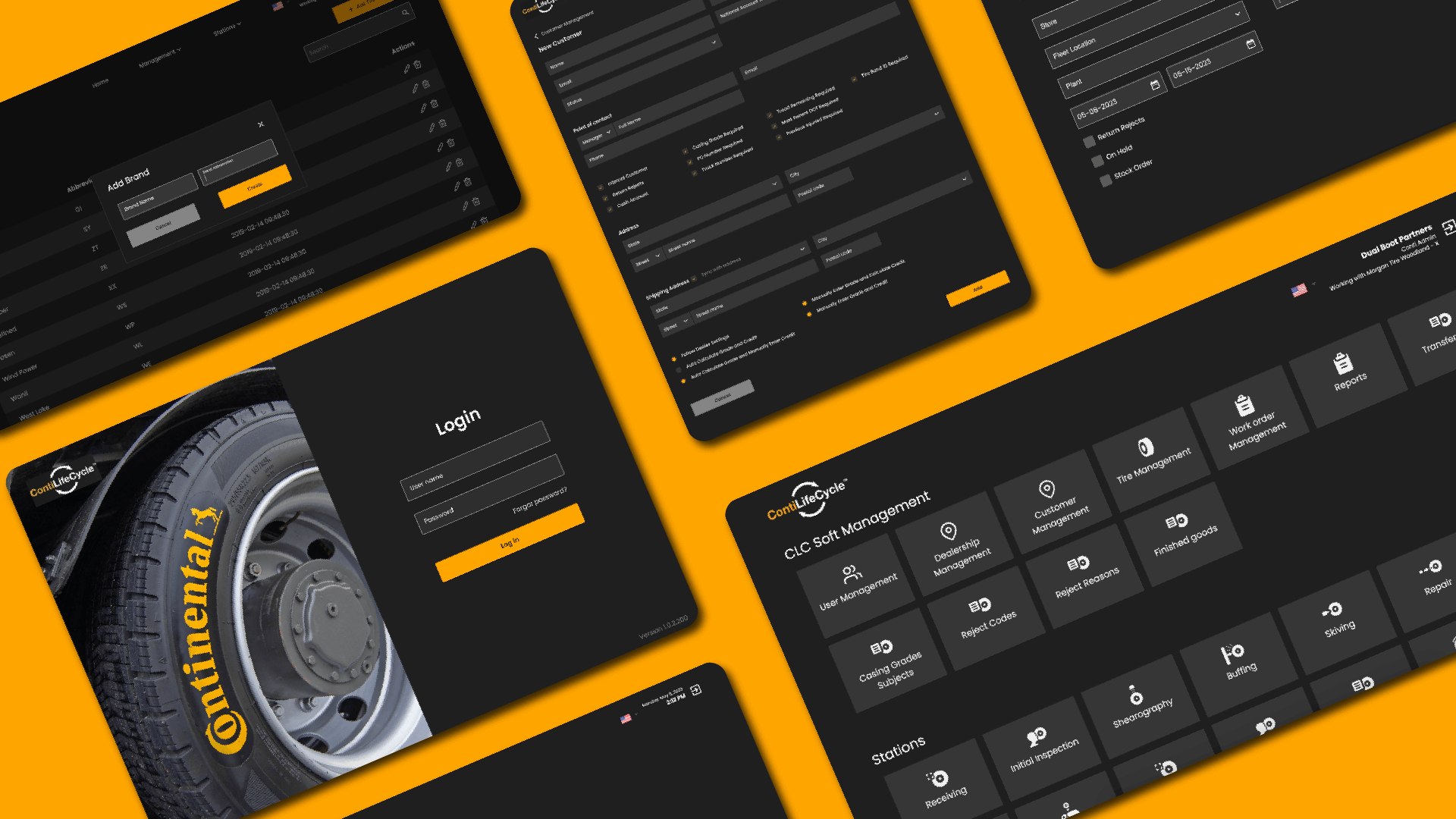
The solution
The ContiLifeCycle app is accessed throughout the multi-stage process with the technician entering data into the computers at each station on the floor. Whether its buffing, repair, hot or cold building or curing, or inspection, each individual retreading station collects and reports data. Plus, each shop had its own specific processes and features from the old application that it relied upon in inventory management and workflow tracking.
Dualboot began its process with an analysis of the existing lifecycle tracking product and discussions with Continental’s stakeholders to identify priorities and opportunities for new functionality. The goal was to enhance reliability and future harden the application.
Along the way with any project, as development continues, Dualboot expects requests to pivot or expand feature offerings. In this case, when a new project manager joined on the client side, the priorities shifted in a big way.
The original plan was to build something to replace the old software, not replicate it. Then, under the new project manager, the goal shifted to replicating every feature of the old platform. It was a big pivot, but Dualboot’s development team built everything that Continental needed. Plus, they did it in time to bring all 13 shops online by the original end of 2023 deadline.
Since each retread location has its own computer systems and siloed data as well as unique processes, bringing each shop online was an added project challenge. Starting with an October visit to a retread shop in Indianapolis after the shift finished at 11 p.m. on launch night, Dualboot’s team ensured every shop had its own version of the system deployed by December 2022. Every two weeks another grouping of shops was launched with Dualboot spot-checking, getting feedback, and making updates along the way.
In many cases, the shops run three shifts a day, which means many opportunities for feedback but no great time to deploy. Plus, if something did go wrong, that could stop work for the entire shift. Quality assurance was critical and any changes had a very quick turnaround.
At the same time, since Continental is a multi-national enterprise client, Dualboot’s team might have to collaborate as well with the company’s DevOps team in Germany to troubleshoot. This meant international calls with screen sharing to try and sort out solutions in real time.
In the end, Continental’s platform has turned a corner.
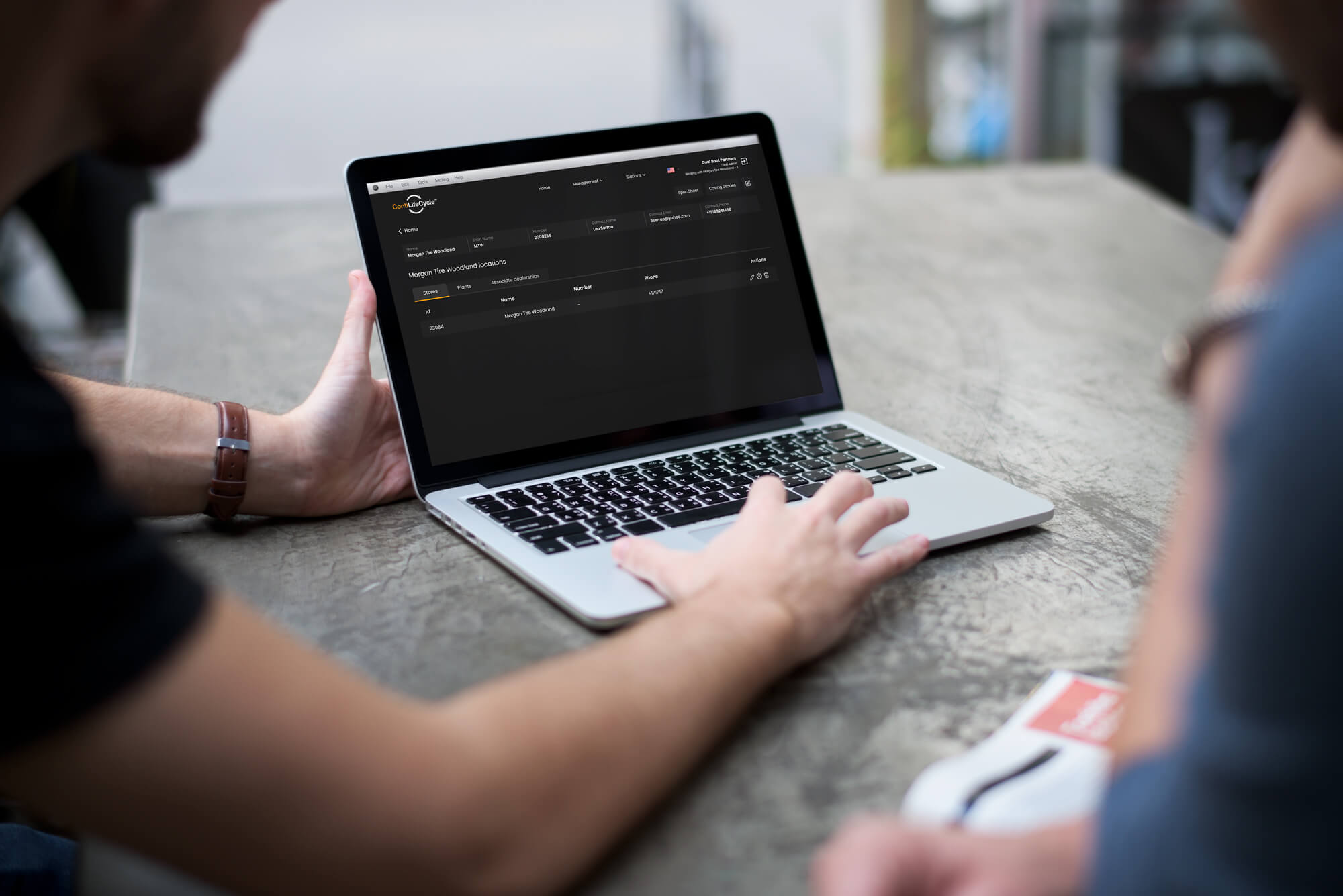
The impact
Continental’s business tagline is “The future in motion.” That’s what Dualboot has enabled with the new offering. In addition to replicating and rebuilding a new system with greater security and a more user-friendly design, the developers also added some priority new features such as balancing scorecards to gauge tire performance, maintenance checklists and in-app user training.
Now the focus is on maintaining the platform and adding in some of the planned features that have not yet gone live. Meanwhile, Continental is discussing the retreading data platform with the company’s overall steering committee to make formal budget decisions about priorities for advancing the application even further as we roll into 2024.